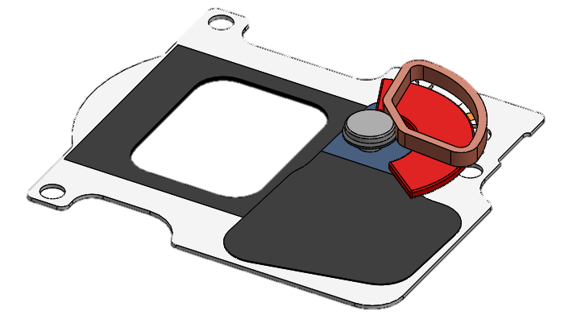
If you are rotating optics or have a requirement for feeding items through and aperture a micro-mechatronic rotary actuator may work best. Combining a direct drive motor, an encoder, motor controller, and precision bearing into one housing creates a solution that is highly accurate, repeatable and very stable.
Precision motion
The combination of a high resolution encoder and digital motor controller results in highly dynamic and accurate positioning or torque control.
Large aperture
Radially thin cross section “ring” motor allows a large aperture. A precision thin cross section bearing centers the shaft while maintaining the large through hole.
Complete system inside the mechanics
Adding the motor controller to the precision assembly results in a complete motion system. Only power and communications inputs are required. The embedded motor controller will servo control the motor based on the encoder signal and execute motion control as well as motor control.
Optional form factors
For mounting and interface sometimes a square assembly is desired. Integrating round motor and bearing components into a precision housing with location features allows for easier special integration.
Low profile
Sometimes it is necessary to insert rotating optics into an existing system. A low profile precision stage can be as thin as 10mm as long as the diameter is available to locate things in plane with the optics.
Special materials
Many optics reside in UV environments. Material selection is critical to have UV compatibility. Special cables and exposed materials need to be carefully considered.
Micro-Mechatronic Rotary Actuator
Applications in advanced electronics and optics require precision and special motion as well as operation in special environments. Sierramotion will guide you through the maze of options and help you settle on the correct design for the project. It is more important for our engineers to help customers with the right solution rather than sell them on what is available.
Specifications | |
---|---|
Low profile | Axial length is minimized for slim integration |
Large aperture | Fit optical components inside the motor |
Optimized performance | Electrically tailored to the input voltage and communications (Ethercat, CAN options) |
Smooth motion | With the proper selection of direct drive motor motion can be smooth without cogging |
High resolution | Using a precision encoder with over 20 bits of rotary resolution |
High accuracy | Accuracy can be measured in arc-seconds based on proper selection of the encoder |
Customized to the need | The mechanical interface and electrical interface can be altered to suit the need |
Frequently asked questions
A rotary stage is essentially a motor with precision bearings, highly precise machined parts, and usually a high accuracy and high resolution encoder.
In many cases yes. However, the direct drive motor’s bearings and precision need to be reviewed. Compared to a precision rotary stage, the motor may not have the accuracy and precision
They are usually marketed to position or run slowly for scanning. However, with the proper slection of the motor, encoder and driver, stages can run up to 3000 rpm. Above this speed, would require a change in bearing selection.
Air bearings offer a level of precision above rotary bearings, they are also very efficient with minimum drag. For ultimate smoothness an air bearing is a good choice, but you would not want to use one for smoothness without also selecting a good smooth zero cogging motor.
Most available stages were designed for some specific application. The reason to customize may be driven by size, weight, precision, performance or materials. Any one of these attributes may drive a decision to customize the solution.