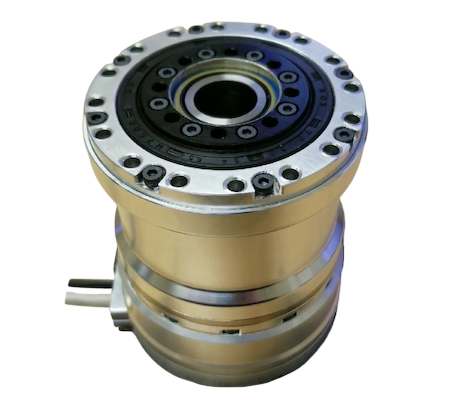
The SMRT-2000 combines a zero backlash high ratio gear with frameless torque motor and absolute encoder all integrated into one assembly. The unit is designed for high torque density and fine control in robotic applications and contains a through hole for wires and other items feeding the distal end of the robot. A high torque frameless torque motor is used for wide speed range and high performance. The absolute encoder has 19 bits of resolution used for both motor commutation and servo positioning. Whether it is a traditional geared motor project or a precision collaborative robot, this highly integrated solution with low weight and low axial profile is highly desirable.
High Torque/Weight
The SMRT-2000 produces up to 50 NM/Kg output of usable torque with full servo positioning control capability utilizing the internal encoder.
Low profile
Most robot joints and gear are compiled from gearboxes and traditional servo motors that are long. This makes them unusable for some robot and collaborative robot projects. The SMRT-2000 is a low profile package that is almost the same length as its diameter. A lot of performance in a small package.
High Accuracy and Repeatability
Combining a high ration precision gear with a high resolution absolute encoder can create more than 50 million counts per revolution. Repeatablity is equal to this resolution and accuracy can be in the arc minute range. If more accuracy and absolute position are required at the joint, then a second absolute encoder can be added to the gear output.
Industry Standard Interfaces
An industry standard 3 phase torque motor will work with any brushless DC or servo driver. The Absolute encoder has a BISSC interface for serial synchronous communication to drivers and host controllers. Simple and effective.
High Gear Ratio and Zero Backlash
Utilizing a precision gear with Orbital Flex Technology allows a ratio of 60:1 up to 150:1 in a small package. Much more attractive size and weight compared to planetary gearing and much higher accuracy. High ratio also mitigates the effects of high inertia variations seen in most robot applications because the reflected inertia is reduced by the square of the gear ration.
Precision torque control
Servo control from the motor and encoder results in high dynamic response, full reversing, precision profiling. If desired, Sierramotion can add a servo driver internal to the SMRT-2000 hosing allowing power and communication connections only. Ethercat options are available if the drive is embedded.
SMRT-2000 Specifications
High torque, low weight, small size, and high performance is at the click of your mouse (or finger). Adjustable input voltage, compatibility with industry standard interfaces makes integration easy.
OD 75mm, Ratio 50:1 | OD 86mm, Ratio 60:1 | OD 97mm, Ratio 70:1 | |
Rated Output Torque | 15 Nm | 45 Nm | 75 Nm |
Repeatable Peak Output Torque | 40 Nm | 75 Nm | 120 Nm |
Rated Input Speed* | 2000 RPM | 2000 RPM | 2000 RPM |
Repeatable Peak Input Speed* | 4000 RPM | 4000 RPM | 4000 RPM |
Efficiency* | 65% | 65% | 65% |
Backlash** | 0 Arcsec | 0 Arcsec | 0 Arcsec |
Positional Accuracy (One-Way) | 3 Arcmin | 2 Arcmin | 2 Arcmin |
Noise*** | 70 dB | 70 dB | 70 dB |
Need a modified or custom solution? Send us an inquiry and we would be happy to discuss. | |||
*Under defined conditions, ** Measured at less than 18 Arcsec, *** Noise at rated speed in ambient room |
Frequently asked questions
Direct drive is gaining in popularity for projects moving light weight items around. Gearing is dominant when it comes to a wide range of robot travel, wide changes in inertia, and payloads above 5 kg.
Very confusing terms, accuracy is how well you move to a place in space. Resolution is how many places in space you can move to. It is entirely possible to have higher resolution than accuracy. It is repeatability that is most important for most projects, and it is equal to the resolution for most systems.
Absolute encoders are hands down a better solution for all but the super high speed projects. Knowing where the system is when powered up is critical. Over travel, homes switches, and many other sensor are not required when you have absolute positioning.
Yes, any gearing will disconnect the input from the output. If you are trying to control precise motion then absolute output position is required. It is also a safety issue and not advised to have mechanical parts in between the output and the measurement.
Heat is a concern when multiple items generating heat are all packaged together. Most designer are conservative in this area and have taken into account derating the motor so that other items can generate heat and all live comfortably inside the same package.