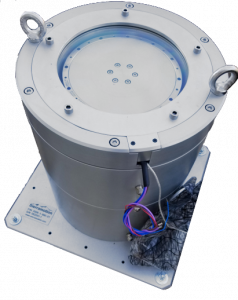
Custom motors are available for specific application needs. Whether it is a unique form factor shape, or performance requirement, Sierramotion designs and produces a product to exactly fit the requirement. With years of experience and more than 2000 motors designed with the same magnetic modelling tools, final build accuracy is +/- 5% of the design targets.
Limited angle, limited travel, rotary motors, linear motors, specialty actuators, motion systems and robotic joints can all be created to meet requirements. With modern techniques for rapid prototyping, a custom motor can be in your hands in less than 8 weeks. Many designs are already available and can be modified to meet many of the requirements with an even faster lead time.
The best end result starts with a good set of requirements. Sierramotion has the experience to review the needs and fill in the blanks covering hidden requirements not identified. This is where most projects fail because some parameter was not on a “datasheet” and didn’t get factored into the requirement. Sierramotion uses years of application engineering experience to avoid problems.
Quick Design Turnaround
Design time includes refining the specification, designing, and getting documents ready for production. Typical design time is < 2 weeks and can be as short at 2 days.
Special Environments
Vacuum, Extreme Ultraviolet Vacuum, Partial Hydrogen, Water, and Blood are all environments Sierramotion has designed motors to operate in. Material selection all the way down to epoxies and material coatings need to be evaluated to insure reliability and performance.
Low Weight
Minimizing weight is done by optimizing the magnetic structure and coil volume. Higher pole counts can increase efficiency at lower operating speeds and also minimize motor weight.
Special Materials and Cleaning
It is common for motors to be used in Space, or in harsh environments. Sometimes it takes alternate materials to handle environmental conditions, such as stainless steel parts.
High Temperatures
Temperatures up to and above 200 Deg C are possible with the proper selection of materials, including insulation and magnets. Sometimes high reliability means designing for high temperature even when you don’t expect high temperature. Low temperature down to -70 C.
Medical rated including the Human Body
Hermetically sealing of motor components. Depending on the application this may include enclosing motor magnets and coils. The appropriate material types and processes for enclosing with Titanium and Stainless include laser welded (and leak tested). Motors for Autoclave sterilization.
Custom Motor specifications
Motor configurations range from 8 mm diameters to 2 meters in diameter, and low profile linear down to 5 mm high. Large motors are typically modular in construction using arc-shaped segments. Axial flux motors up to and beyond 2 meters in diameter or rotating gantry stages. Sierramotion will discuss the requirements with you and arrive at both mechanical and electrical parameters while predicting torque, speed, efficiency and other performance attributes.
Specifications | |
---|---|
Diameter | 8 mm-2 meter |
Length | 3 mm to 100 mm |
Modular construction | Arc segments or linear segments |
Vacuum | 10-9 Torr |
Space | Space Radiation rated |
High Temperatures | 200°C |
Low Temperatures | -70°C |
High torque constant | Optimized for low speed operation |
Low voltage constant | For low voltage and high speed operation |
Frequently asked questions
Design time typically takes 1-2 weeks and fabrication 6-8 weeks.
Almost everything including mechanical size, materials, magnetic output, speed, torque, smoothness, acceleration can be modified. Fit the motor to the application, not the application to the motor.
The cost for designing and customizing has reached historically low levels. Design tools and tooling have greatly improved. A motor can be designed on a smart phone and new manufacturing techniques are used to curb tooling costs. Custom motors are no longer more expensive than other available motors. Suppliers are not stocking finished goods these days, and some components are hard to get making standard lead times long.
Yes, mechanical parts can be die-cast, magnets can be molded, even motor iron can be fabrication with SMC (sintered metal compound). The viability of using these processes depends on the project.
Permanent magnet motors can also be used as generators. The voltage output is proportional to speed and power is proportional to current flowing in the generator. Many applications utilize motors as generators and some even switch between motoring and generating on the fly.