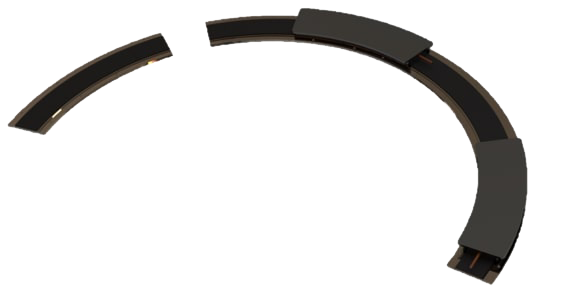
Frameless motors are actually the magnetic portion of a traditional motor. The magnet portion is comprised of two parts, a stator and a rotor. The stator has electromagnetic phases and the rotor has permanent magnets attached (or more electromagnetic phases as in an AC Induction motor). All traditional housed motors have a frameless motor kit inside them. Some non-tradition assemblies like Gimbals house frameless motors where the mechanical structure and bearings support the stator and rotor.
Frameless motors are typically used in direct drive applications and tend to be large in diameter and short in axial length. Most of them have a large through hole and a high pole count. This combination of attributes allow them to excel at direct drive and offer options for optics or cables to flow through the aperture of the motor.
High Torque and high Km (motor constant)
Designs that optimize the torque output and minimize weight tend to provide good direct drive torque control.
Frameless motors with gearing
Normally they are used in direct drive, but they are also widely used in robotic applications connected to a high ration zero backlash gearing system. This combination results in a very low profile high torque robot joint.
Short axial length (low profile)
Based on the motor technology used, frameless motors can get to down to less than 5mm in axial length, while having diameters from 50-500mm as the same time. This allows a motor to be fit into a tight space and maybe fit between parts that are already in a machine, for example a turret rotation.
High temperature operation
Operating temperatures above 200°C are possible with the correct magnet selection and motor design. Insulation materials and other epoxies and potting compounds can be selected to optimize this.
Low voltage and high windings
Winding options for frameless kits can vary from operation at 5 volts to 600 volts. Lower voltage operation with moderate speeds is tricky and requires special winding configurations. High voltage requires double insulation and special materials selection.
Operation in vacuum
Three options are available, low and dirty vacuum 10E-6 range can be done with special materials and pre-outgassing. Low clean vacuum can be done with epoxy encapsulation. High vacuum < 10E-9 can be done by laser welding a non-magnetic enclosure around the stator and rotor, (if the rotor is also also in a vacuum with Hydrogen purge).
Frameless Motor specifications
Frameless motor are configured quickly to match the size and performance required. Large through holes are typical and the overall form factor can be tailored to the project. Full magnetic models are complete to simulate performance before materials are ordered. With today’s tools a motor design can easily be complete in hours. General lead times are long for “standard” products, and costs have increased for “standard” products, it is really a good time to get a customized solution for the same price and lead time as a “standard” off the shelf solution.
Specifications | |
---|---|
Diameter range | 8mm to 2000mm |
Axial length range | 5mm to 400mm |
Voltage operation | 5 volts to 600 volts |
Temperature range | -50°C to +70°C (with option for 200°C+) |
Vacuum rating | Down to < 9E-9 with proper design |
Radiation hardening | Using laser welded cover |
Torque output | .01 to 1000 NM |
Speed ranges | .0001 rpm to 5000 rpm |
Frequently asked questions
The direct drive application is the main use and in this case a higher pole count can improve torque and efficiency while keeping weight and size down. The electromagnetic frequency of a motor really determines its efficiency versus speed curve. A 4 pole motor will have high efficiency at 10,000 rpm, a 40 pole motor would have the same electrical frequency at 1000 rpm. High pole count is like an electromagnetic gear ratio.
Yes, but typical servo motors are long and have small diameters and low pole counts. This may work, but frameless motor kits tend to be short in length large in diameter and have high pole count – better for direct drive applications.
Yes, and many people do this. In the case of a Camera Gimbal on an UAV, there may be a reason to hold position and provide torque against a windage load. Torque control is one of the main reasons for direct drive applications, frameless motors are generally good at this.
Not all of the motors are smootly running. Many have cogging torque and torque ripple. The smoothest running motors are slotless frameless motors with zero cogging. The slotless motor also has very linear torque with current making it optimum for torque control applications.
Yes, but the slotless version is the best for this because torque is linear with current, there is no cogging, and torque ripple when commutating is very low. Most traditional iron core motors have cogging torque and torque is non-linear with current (saturation) making them too non-linear to be used as torque sensors or in haptic applications.
There really is not much difference. Many suppliers call their frameless motors “torque motors” while trying to differentiate their motor. It is all too often that supplier mix up the form of the motor with the function of the motor and name it incorrectly, just confusing the customer.