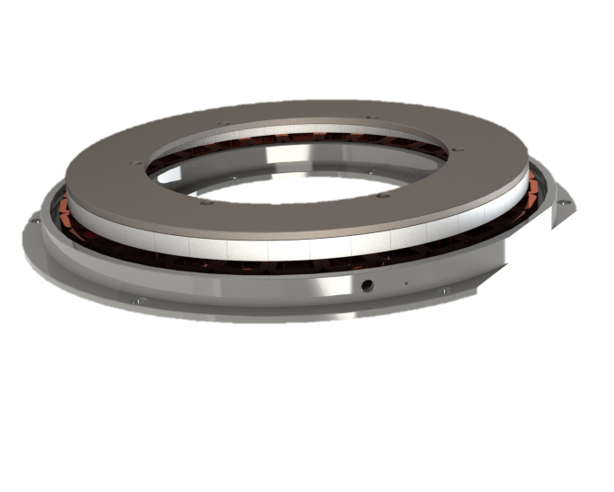
Sierramotion routinely optimizes motors for operating in vacuum. This includes proper material selection, hermetic sealing for deep vacuum <10-7 bar, and thermal restrictions due to operating in vacuum. Space rating is generally different than vacuum rating for a motor. The difference is normally radiation effects and temperature effects of being in space. Precision advanced industrial machines with vacuum chambers generally care about outgassing.
Fully enclosed and hermetically sealed
If deep vacuum, or a special vacuum environment is required. Hermetically sealing the motor components it the best solution. Sierramotion will design the motor to including a hermetic laser welded enclosure.
Options electrical windings
Thermal limitations tend to drive electrical optimization. Sierramotion can change the motor winding to minimize current and maximize efficiency for a vacuum specific application.
Thermal sensor options
he best option for controlling temperature is to use the correct thermal sensor. Sometimes, a thermal switch is not recommended because it gives not early warning. A thermal sensor that can be continuously monitored is best.
Good conduction paths
When operating in vacuum there is no convection, so conduction path and minimizing thermal resistance is critical. Thermal modelling is sometimes necessary in order to get the best materials and minimize the thermal resistance of each interface.
Special encapsulation for good thermal conduction
Since the vacuum environment thrives on conduction over convection, encapsulating the motor with a thermally conductive epoxy will provide the best path from the motor winding to the iron case.
Vacuum feedthrough options
If operating in deep vacuum, a wire feedthrough is necessary along with the hermitic enclosure. Glass based vacuum feedthroughs are selected and laser welded into the housing during the enclosure process.
Vacuum Motor specifications
Specifications | |
---|---|
Moderate vacuum | 10-7 bar can be done with encapsulant |
Deep Vacuum | 10-9 bar+ requires enclosure |
Low thermal resitance | Optimize conduction paths |
Material options | Optimize for special environments like UV, EUV, Hydrogen, etc. |
Options motor windings | Adjust electrical to optimize efficiency |
Stainless enclosures | Cover all of the magnets and stator windings |
Optional magnet grades | Limit temperature rise with a modified magnetic design that accounts for the enclosure |
Frequently asked questions
Yes, but it may result in contamination of the vacuum environment and the motor may overheat because its rating was based on an atmospheric thermal test. If the goal is to put a motor in space, maybe outgassing isn’t an issue, but other factors like temperature, radiation etc. can limit use.
See Motors for Vacuum Envioronments for more informtion.
One that is designed for the environment with proper materials, magnetic design, housing, and thermal rating. This is an easy problem to solve, unfortunately not many first-time users realize the difficulty working in a vacuum.
Magnets are typically formed by pressing magnetic particles into a shape. Unfortunately, rare earth magnets do not stank up to Hydrogen and actually disintegrate. If there is any Hydrogen in the vacuum magnets need to be hermetically sealed.
Yes. The motor needs to be sized correctly to the load and the lack of thermal convection needs to be factored in. Some motors need to be de-rated up to 50% for vacuum environments. If the motor parts are enclosed in a housing, then magnetic efficiency gets reduced and additional de-rating of 20% may be the result.
Yes, and that is a good way to separate motor materials like magnets and copper wire from the vacuum chamber. A magnetic coupling can bridge the wall of the chamber and be driven from the external motor. Internally everything can be vacuum compatible, even an encoder can be used if vacuum rated.